Summary:
Boosting Productivity: The Role of Palletising in Supply Chain Management
Historical Evolution of Palletising Techniques
Significance of Palletising in Modern Supply Chains
Benefits of Palletising in Supply Chain Management
In the supply chain, pallet stacking is a critical logistics operation that involves stacking and organizing goods on pallets for more efficient storage, transportation, and loading and unloading. This process plays an important role in improving the efficiency of the supply chain and reducing costs. Let’s delve deeper into the key aspects of pallet stacking in the supply chain.
Pallet stacking refers to the use of pallets in the supply chain to stack and arrange goods in a certain way for transportation, storage, and sorting. This involves cleverly organizing goods to maximize space utilization and optimize logistics processes.
Stacking technology
There are multiple technologies and methods to choose from during the pallet stacking process. This may include the application of manual stacking, automated stacking systems, and robotics technology. Having a deep understanding of these technologies will help businesses choose the stacking solution that best suits their needs.
Optimize storage space
By cleverly stacking pallets, enterprises can maximize the optimization of storage space. This not only helps to reduce warehousing costs, but also improves the accessibility of inventory, reducing damage and waste of goods.
Improved transportation efficiency
Pallet stacking is equally crucial for the transportation of goods. Reasonable pallet stacking can reduce the risk of damage during transportation, lower transportation costs, and improve delivery efficiency.
Intelligence and data-driven
Modern supply chains are increasingly inclined towards intelligent and data-driven solutions. Pallet stacking is no exception. By using sensors, the Internet of Things, and data analysis, enterprises can achieve real-time monitoring and optimization of the stacking process.
Pallet stacking in the supply chain is a complex and important process that directly affects the efficiency and overall operation of the supply chain. By adopting advanced technologies and strategies, enterprises can maximize the potential of pallet stacking, improve productivity, reduce costs, and ensure the safe and efficient flow of goods throughout the entire supply chain.
Historical Evolution of Palletising Techniques
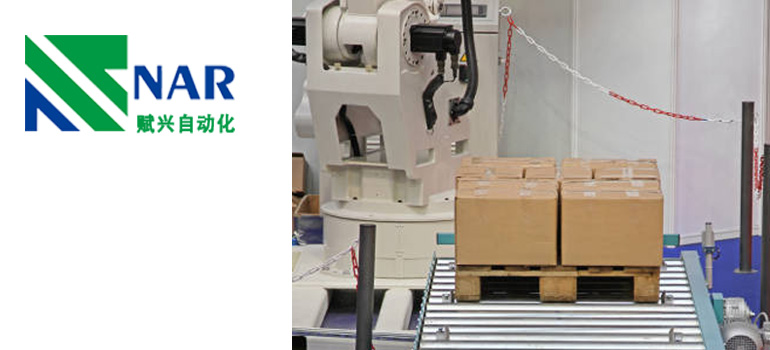
The historical evolution of palletising techniques reflects the continuous efforts to enhance efficiency and streamline logistics processes within the supply chain. Let’s take a journey through the development of palletising techniques over time:
Early Stacking Methods
In the early days of logistics, manual stacking and arranging goods for transportation were common practices. Workers would manually load and unload individual items onto and from transport vehicles. This method, although labor-intensive, laid the foundation for understanding the importance of organized cargo handling.
Introduction of Wooden Pallets
The mid-20th century witnessed a significant shift with the introduction of wooden pallets. Wooden pallets provided a standardized and durable platform for stacking goods. This innovation not only facilitated easier loading and unloading but also allowed for the use of forklifts, automating parts of the process and reducing manual labor.
Palletising Automation
As technology advanced, the latter half of the 20th century saw the emergence of automated palletising systems. Companies began adopting conveyor belts, robotic arms, and other mechanized solutions to palletise goods more efficiently. Automation not only increased speed but also improved accuracy in the stacking process.
Plastic and Metal Pallets
In the late 20th century and into the 21st century, the materials used for pallets diversified. Plastic and metal pallets gained popularity due to their durability, cleanliness, and reusability. This shift allowed for a more sustainable approach to palletising while addressing concerns about pests, hygiene, and weight restrictions associated with wooden pallets.
Integration of Robotics and AI
In recent years, there has been a surge in the integration of robotics and artificial intelligence (AI) in palletising. Advanced robotic palletising systems can adapt to various product shapes and sizes, optimizing the stacking process. AI algorithms contribute to real-time decision-making, improving the overall efficiency and adaptability of palletising techniques.
Data-Driven Optimization
The current trend involves leveraging data analytics and the Internet of Things (IoT) for data-driven palletising optimization. Sensors and smart technologies enable continuous monitoring of palletising operations, providing insights into performance, inventory levels, and potential areas for improvement.
The historical evolution of palletising techniques reflects a journey from manual labor to advanced automation and data-driven optimization. Each phase has contributed to increasing efficiency, reducing costs, and ensuring the smooth flow of goods in the supply chain. As technology continues to advance, the future of palletising may involve even more sophisticated and adaptive solutions.
Significance of Palletising in Modern Supply Chains
The significance of palletising in modern supply chains cannot be overstated, as it plays a pivotal role in enhancing efficiency, reducing costs, and ensuring the smooth flow of goods from production to distribution. Let’s delve into the key aspects that highlight the importance of palletising in the context of contemporary supply chain management:
Optimized Storage and Warehousing:
Palletising allows for efficient use of warehouse space by organizing goods in a structured manner. Stacking products on pallets enables vertical storage, maximizing the available space and facilitating easy access during retrieval. This optimization contributes to reduced storage costs and improved inventory management.
Streamlined Material Handling:
Palletised goods are easily handled using material handling equipment such as forklifts and pallet jacks. This streamlines the loading and unloading processes, reducing manual labor and minimizing the risk of damage to products. The ease of handling also accelerates the overall supply chain operations.
Facilitates Bulk Transportation:
Palletised loads are well-suited for bulk transportation. They enable the consolidation of multiple items into a single unit, making it easier to load and unload shipments. This not only enhances transportation efficiency but also reduces shipping costs by maximizing the use of available cargo space.
Reduces Risk of Damage:
By providing a stable and uniform platform for goods, palletising minimizes the risk of damage during transit. The standardized design of pallets ensures that products remain secure and well-supported, reducing the likelihood of breakage or spoilage. This is particularly crucial for delicate or perishable items.
Enhances Supply Chain Visibility:
Palletising contributes to improved supply chain visibility. Standardized pallets make it easier to track and trace products throughout the supply chain. This visibility is vital for inventory management, order fulfillment, and meeting customer demands in a timely and accurate manner.
Supports Automation and Technology Integration:
Modern palletising techniques seamlessly integrate with automation and technology. Automated palletising systems and robotics enhance the speed and accuracy of stacking, further reducing reliance on manual labor. This integration aligns with the broader trend of Industry 4.0 in supply chain management.
Promotes Sustainability:
The use of reusable pallets and the optimization of transportation contribute to sustainability efforts. Palletising minimizes packaging waste, as goods can be secured on the pallet without excessive use of additional materials. Additionally, efficient transportation reduces the carbon footprint associated with logistics operations.
In the modern supply chain landscape, palletising emerges as a cornerstone for efficiency, cost-effectiveness, and sustainability. Its significance extends across various stages of the supply chain, from storage and transportation to automation and visibility. As supply chains continue to evolve, palletising remains a fundamental practice for optimizing logistics operations and meeting the demands of a dynamic market.
Benefits of Palletising in Supply Chain Management
Palletising in supply chain management offers a multitude of benefits that contribute to improved efficiency, cost-effectiveness, and overall optimization of logistics processes. Let’s explore the key advantages of incorporating palletising into supply chain management:
Efficient Handling and Transportation:
Faster Loading and Unloading: Palletised goods can be quickly loaded and unloaded using forklifts or pallet jacks, reducing handling time and labor requirements.
Bulk Transportation: Pallets facilitate the transportation of multiple products as a single unit, maximizing cargo space and enhancing efficiency in shipping.
Optimized Storage and Warehousing:
Space Utilization: Palletising allows for efficient use of warehouse space by stacking products vertically. This optimization results in reduced storage costs and improved inventory management.
Easy Retrieval: Well-organized pallets make it easier to locate and retrieve specific products from the warehouse, streamlining order fulfillment processes.
Reduced Risk of Damage:
Product Stability: Pallets provide a stable platform for goods, reducing the risk of damage during transit. This is particularly crucial for fragile or sensitive products.
Secure Packaging: Products on pallets can be securely wrapped or strapped, further protecting them from damage caused by shifting or rough handling.
Cost Savings:
Labor Efficiency: Palletising minimizes the need for manual labor in handling and moving goods, leading to labor cost savings.
Transportation Costs: Consolidating goods on pallets optimizes cargo space, reducing the number of trips required for transportation and lowering overall shipping costs.
Supply Chain Visibility and Traceability:
Trackability: Palletised goods are easier to track and trace throughout the supply chain, enhancing visibility and transparency in inventory management.
Real-time Monitoring: Integration with technology allows for real-time monitoring of pallet movements, enabling better decision-making and responsiveness.
Facilitation of Automation:
Integration with Robotics: Palletising aligns with automation trends, allowing for the integration of robotic systems to further enhance stacking speed and accuracy.
Industry 4.0 Compatibility: Automated palletising systems contribute to the adoption of Industry 4.0 practices in supply chain management.
Environmentally Friendly Practices:
Reusable Pallets: The use of reusable pallets contributes to sustainability efforts by minimizing packaging waste.
Reduced Carbon Footprint: Efficient transportation and logistics operations associated with palletising contribute to a reduced carbon footprint.
Palletising in supply chain management is not just a logistical technique, it is a strategic approach that brings about a range of benefits, from operational efficiency to environmental sustainability. By embracing palletising, businesses can position themselves for streamlined logistics, reduced costs, and enhanced competitiveness in the dynamic landscape of modern supply chains.