In today’s fast-paced business world, optimizing operations is key to staying ahead of the competition. One of the most fundamental aspects of business operations is the movement of materials, products, and equipment. The process of moving materials from one location to another is known as material handling, and it is a critical component of many different industries.
When it comes to material handling, there are two primary methods: manual VS automated material handling.
In this article, we’ll focus on manual material handling systems, exploring what they are, how they work, and what advantages they offer for businesses.
Muscle Up: Understanding the Ins and Outs of Manual Material Handling Systems
What Is a Manual Material Handling System?
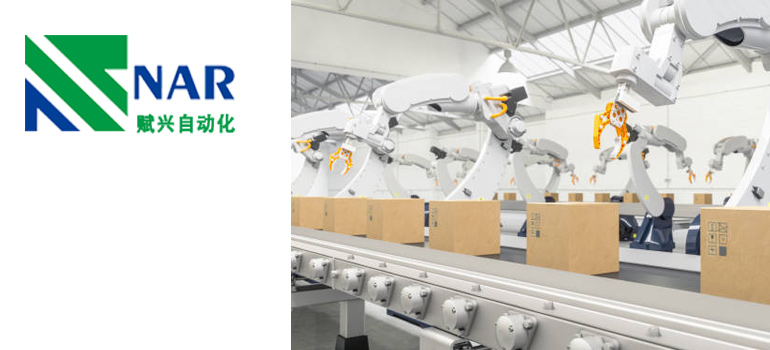
Manual material handling systems rely on human labor to move, lift, and transport materials or products from one location to another. These systems typically involve the use of carts, dollies, hand trucks, or other equipment, as well as physical exertion by workers.
Manual material handling systems can be as simple as a single worker pushing a cart of materials, or as complex as a team of workers using specialized equipment to move heavy or awkwardly shaped objects. These systems require workers to use proper lifting and handling techniques to avoid injury, and they may also involve the use of personal protective equipment such as gloves or back braces.
The Power of People: Exploring the Advantages of Manual Material Handling Systems
While automated material handling systems offer several advantages, manual material handling systems still have a significant role to play in many business operations. By prioritizing flexibility, affordability, safety, improved ergonomics, and customization, businesses can create efficient and effective material handling systems that meet their specific needs and requirements:
- Flexibility and Adaptability: One of the primary advantages of manual material handling systems is their flexibility and adaptability. Unlike automated systems, which are often designed for specific tasks or products, manual systems can be adjusted and modified to fit the specific needs and requirements of the operation. This means that businesses can easily adapt to changing needs or product lines without significant investments in new technology or equipment.
- Affordability: Another advantage of manual material handling systems is their affordability. Since manual systems require less specialized equipment and technology than automated systems, they are often more affordable to implement and maintain. This can be a significant advantage for small or medium-sized businesses with limited resources or budgets.
- Safety: Manual material handling systems also offer several safety benefits. Since workers are responsible for physically handling and moving materials or products, they can be more aware of potential hazards and risks. This can reduce the risk of accidents or injuries, and improve overall safety in the workplace.
- Improved Ergonomics: Manual material handling systems can also improve ergonomics in the workplace. By utilizing proper lifting techniques and ergonomic equipment, workers can reduce the risk of musculoskeletal disorders and injuries. This can lead to increased productivity, improved employee morale, and reduced workers’ compensation costs.
- Customization: Finally, manual material handling systems offer a high degree of customization. Since these systems are typically less complex than automated systems, they can be easily modified and adapted to fit the unique needs and requirements of a business. This means that businesses can create customized material handling solutions that are optimized for their specific needs and workflows.
Whether a business chooses a manual or automated system, the key is to choose a solution that optimizes productivity, safety, and profitability.
Rise of the Machines: The Rise of Automated Material Handling Systems in Business Operations
As technology continues to advance, businesses are increasingly turning to automated material handling systems to streamline their operations. These systems use a combination of specialized equipment, sensors, and software to move and manipulate products or materials throughout the supply chain.
One of the primary advantages of automated material handling systems is their ability to operate continuously and consistently, without the need for breaks or rest periods. This can lead to increased productivity and efficiency, as well as improved accuracy and precision in handling tasks.
Automated systems can also reduce the risk of workplace injuries and accidents. By removing the need for human workers to perform physically demanding tasks, businesses can minimize the risk of musculoskeletal disorders and other injuries. Additionally, automated systems can be programmed to identify potential safety hazards and take corrective action to prevent accidents.
Another advantage of automated material handling systems is their scalability. As businesses grow and expand their operations, automated systems can be easily modified or expanded to accommodate the increased volume of products or materials. This can help businesses to avoid costly investments in additional equipment or facilities.
However, it’s important to note that automated material handling systems can come with a higher initial investment and ongoing maintenance costs compared to manual systems. Additionally, they may not offer the same level of flexibility and adaptability as manual systems.
The Future Is Here: Discovering the Benefits of Automated Material Handling Systems
As technology continues to evolve, automated material handling systems are becoming increasingly sophisticated, offering businesses a wide range of benefits and advantages.
Let’s take a closer look at some of the most significant benefits of these advanced systems:
Increased Efficiency and Productivity
- Automated material handling systems can significantly increase efficiency and productivity by reducing the need for manual labor and streamlining operations. They can handle large volumes of products or materials quickly and accurately, without the risk of human error.
Enhanced Safety
- Automated material handling systems can improve safety by reducing the risk of accidents and injuries associated with manual labor. These systems are designed with advanced safety features, such as sensors and alarms, to prevent collisions and other hazards.
Improved Quality Control
- Automated material handling systems can help businesses to maintain consistent product quality by ensuring that products are handled and processed according to precise specifications. This can help to minimize errors and defects, leading to higher customer satisfaction rates.
Cost Savings
- While automated material handling systems may require a higher initial investment, they can ultimately lead to significant cost savings over time.These systems can also improve safety in the workplace by reducing the risk of injuries caused by repetitive tasks or heavy lifting.
Increase accuracy in material handling
- This is especially important in industries that deal with fragile or hazardous materials.
Ability to operate 24/7 without the need for breaks or rest periods
- Sgnificantly increase productivity and reduce labor costs. These systems can also be programmed to perform tasks with a high level of precision and consistency, reducing the risk of errors and increasing overall efficiency.
In addition, automated material handling systems can be integrated with other technologies, such as inventory management systems and warehouse management software, to create a fully automated supply chain. This can provide businesses with real-time data on inventory levels, order status, and shipping information, allowing them to make more informed decisions and respond quickly to changes in demand.
Furthermore, the use of automated material handling systems can help businesses reduce their environmental impact by optimizing energy usage and reducing waste. For example, automated systems can be programmed to conserve energy during periods of low activity, and they can also help reduce the amount of packaging materials required for shipping and handling.
Manual VS Automated Material Handling? The Ultimate Showdown of Efficiency, Safety, and Cost
Manual or automated material handling? It’s the ultimate showdown for businesses looking to boost efficiency, safety, and cut costs. On one hand, manual handling offers flexibility and a personal touch, but it’s prone to errors and injuries. On the other hand, automated handling offers precision and consistency, but it can be rigid and expensive.
When it comes to efficiency, safety, and cost, each approach has its pros and cons. Automated handling can be faster and more cost-effective in the long run, but it requires a big investment upfront. Manual handling may seem cheaper at first, but it can lead to higher labor costs and risks of injury.
In the end, there is no one-size-fits-all answer. The decision between manual VS automated material handling depends on the specific needs of your business. You may even find that a hybrid approach is the best solution for you.
So, which one will it be?
Whether you go manual or automated, the key is to choose the approach that maximizes efficiency, safety, and cost-effectiveness for your business.
The choice is yours!