Summary:
Maximizing Output: The Advantages of Automated Packaging Machinery
Streamlining Production Processes with Automated Packaging Machinery
Optimizing Labor Utilization and Resource Allocation
Improved Quality Control Measures
Cost-Efficiency and Return on Investment (ROI)
Streamlining Production Processes with Automated Packaging Machinery
Automated packaging machinery has revolutionized production processes by streamlining various stages of packaging, from product handling to labeling. Let’s delve into how these systems optimize efficiency:
Reduced Labor Dependency: Automated packaging machinery significantly reduces the reliance on manual labor for packaging tasks. By automating repetitive and labor-intensive processes such as product sorting, filling, sealing, and labeling, these systems minimize the need for human intervention. This not only lowers labor costs but also frees up personnel to focus on higher-value tasks such as quality control and process optimization.
Increased Speed and Throughput: One of the most notable advantages of automated packaging machinery is its ability to operate at high speeds while maintaining precision and accuracy. These systems can process a large volume of products in a fraction of the time it would take manually, leading to a substantial increase in throughput. This accelerated pace of packaging not only boosts production output but also allows companies to meet tight deadlines and respond quickly to fluctuating market demands.
Enhanced Consistency and Quality Control: Automated packaging machinery ensures consistent and uniform packaging results with minimal variation. By adhering to predefined settings and parameters, these systems consistently produce packages that meet strict quality standards and specifications. This consistency is crucial for brand reputation and customer satisfaction, as it eliminates variability and ensures that every product meets the same high-quality standards.
Optimized Material Usage and Waste Reduction: Automated packaging machinery optimizes material usage by precisely controlling the amount of packaging material required for each product. By minimizing overuse and waste, these systems help reduce costs associated with packaging materials while minimizing environmental impact. Additionally, advanced features such as automatic defect detection and rejection help identify and discard defective packages, further minimizing waste and maximizing product quality.
Seamless Integration and Workflow Efficiency: Automated packaging machinery seamlessly integrates into existing production lines, enhancing overall workflow efficiency. These systems can be synchronized with upstream and downstream equipment, such as filling machines, labeling systems, and palletizers, to create a continuous and streamlined packaging process. This integration eliminates bottlenecks, reduces downtime, and improves overall equipment effectiveness (OEE), resulting in a more efficient and productive operation.
Optimizing Labor Utilization and Resource Allocation
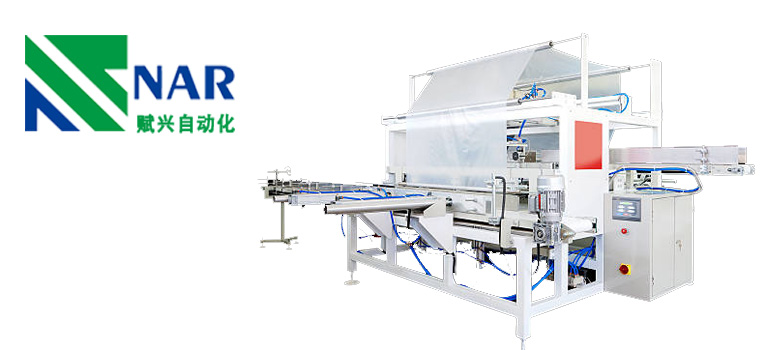
Optimizing labor utilization and resource allocation is a crucial aspect of implementing automated packaging machinery. Here’s how these systems contribute to efficient resource management:
Labor Efficiency: Automated packaging machinery reduces the reliance on manual labor, allowing companies to optimize their workforce and allocate personnel to more strategic and value-added tasks. By automating repetitive and labor-intensive packaging processes such as product loading, sealing, and labeling, these systems minimize the need for human intervention, freeing up employees to focus on tasks that require creativity, problem-solving, and decision-making.
Resource Allocation: Automated packaging machinery optimizes the allocation of resources, including materials, energy, and equipment. By precisely controlling the amount of packaging material used for each product and minimizing waste, these systems help reduce material costs and environmental impact. Additionally, automated processes consume less energy compared to manual operations, contributing to overall energy efficiency and sustainability. Moreover, by streamlining production processes and minimizing downtime, automated packaging machinery maximizes the utilization of equipment and facilities, ensuring optimal resource allocation across the organization.
Training and Skill Enhancement: With automated packaging machinery handling routine tasks, employees can focus on developing specialized skills and expertise that are essential for managing and maintaining advanced packaging systems. Companies can invest in training programs to upskill their workforce and empower employees to operate and troubleshoot automated equipment effectively. This not only enhances employee engagement and job satisfaction but also creates a more skilled and adaptable workforce capable of driving continuous improvement and innovation in packaging operations.
Safety and Ergonomics: Automated packaging machinery contributes to a safer and healthier work environment by reducing the risk of injuries associated with manual handling of heavy loads and repetitive tasks. By automating physically demanding and hazardous tasks, these systems minimize the likelihood of workplace accidents and musculoskeletal disorders, improving employee safety and well-being. Additionally, ergonomic design features such as adjustable height controls and safety guards further enhance workplace ergonomics, ensuring comfortable and safe working conditions for employees.
Scalability and Adaptability: Automated packaging machinery offers scalability and adaptability to meet changing production demands and market requirements. Companies can easily adjust production volumes and packaging formats without significant changes to equipment or workforce size. This flexibility enables organizations to respond quickly to market fluctuations, seasonal demand variations, and product diversification, ensuring efficient resource allocation and maintaining competitiveness in dynamic business environments.
Improved Quality Control Measures
Implementing automated packaging machinery brings about significant improvements in quality control measures throughout the packaging process. Let’s delve into how these systems enhance quality control:
Consistency and Uniformity: Automated packaging machinery ensures consistent and uniform packaging results for every product. By adhering to predefined settings and parameters, these systems produce packages with minimal variation in dimensions, appearance, and sealing integrity. This consistency is crucial for maintaining brand reputation and customer satisfaction, as it eliminates variability and ensures that each product meets the same high-quality standards.
Precision and Accuracy: Automated packaging machinery operates with precision and accuracy, minimizing errors and deviations in packaging specifications. These systems are equipped with sensors, cameras, and other inspection devices that detect defects, misalignments, or abnormalities in packaging materials or products. By identifying discrepancies early in the process, automated systems enable corrective actions to be taken promptly, preventing defective products from reaching consumers.
Real-time Monitoring and Feedback: Advanced automated packaging machinery provides real-time monitoring and feedback on packaging performance and product quality. Integrated sensors and monitoring systems continuously track critical parameters such as package weight, seal integrity, barcode readability, and label placement. Any deviations from predefined standards trigger immediate alerts or alarms, prompting operators to take corrective actions and prevent quality issues from escalating.
Traceability and Documentation: Automated packaging machinery facilitates traceability and documentation of packaging processes, ensuring transparency and accountability throughout the supply chain. These systems can record and archive data related to production batches, packaging materials, and quality control inspections. By maintaining comprehensive records and documentation, companies can trace the origin of products, track production history, and respond to quality-related inquiries or regulatory requirements effectively.
Compliance with Standards and Regulations: Automated packaging machinery helps ensure compliance with industry standards, regulatory requirements, and quality assurance protocols. These systems are designed and calibrated to meet or exceed established standards for packaging integrity, safety, and hygiene. By consistently adhering to regulatory requirements and industry best practices, automated packaging machinery helps companies mitigate risks, avoid costly recalls, and maintain regulatory compliance, thus safeguarding brand reputation and consumer trust.
In summary, automated packaging machinery enhances quality control measures by promoting consistency, precision, real-time monitoring, traceability, and compliance throughout the packaging process. These systems play a critical role in safeguarding product quality, integrity, and safety, ultimately contributing to customer satisfaction and brand loyalty.
Cost-Efficiency and Return on Investment (ROI)
Analyzing the cost-efficiency and return on investment (ROI) of automated packaging machinery is crucial for evaluating its financial impact on a business. Let’s explore how these systems contribute to cost savings and generate positive ROI:
Reduced Labor Costs: Automated packaging machinery significantly reduces labor costs by minimizing the need for manual intervention in packaging processes. By automating repetitive and labor-intensive tasks such as product loading, sealing, and labeling, these systems eliminate the need for additional workforce, overtime hours, and associated labor expenses. As a result, companies can achieve substantial savings in labor costs over the long term.
Increased Production Efficiency: Automated packaging machinery improves production efficiency by streamlining packaging processes and minimizing downtime. These systems operate at higher speeds and with greater precision compared to manual operations, resulting in higher throughput and output levels. By maximizing production capacity and minimizing idle time, automated machinery optimizes equipment utilization and generates higher revenue potential for the business.
Lower Material Waste and Overhead: Automated packaging machinery reduces material waste and overhead costs associated with packaging operations. These systems optimize material usage by precisely controlling the amount of packaging material required for each product, minimizing overuse and waste. Additionally, automated processes consume less energy compared to manual operations, leading to reduced utility expenses and lower overhead costs for the business.
Improved Product Quality and Customer Satisfaction: Automated packaging machinery enhances product quality and consistency, leading to higher customer satisfaction and loyalty. By ensuring precise and uniform packaging results, these systems minimize the risk of product defects, rework, and returns, reducing associated costs and preserving brand reputation. Satisfied customers are more likely to repeat purchases and recommend the brand to others, contributing to long-term revenue growth and profitability.
Long-Term Sustainability and Competitiveness: Investing in automated packaging machinery enables companies to achieve long-term sustainability and competitiveness in the market. By leveraging advanced technology and automation, businesses can enhance their operational efficiency, reduce production costs, and adapt quickly to changing market demands. This strategic investment not only generates immediate cost savings and ROI but also positions the company for future growth and expansion in a competitive business landscape.
In summary, automated packaging machinery offers significant cost-efficiency benefits and a positive ROI for businesses by reducing labor costs, increasing production efficiency, minimizing material waste, enhancing product quality, and ensuring long-term sustainability and competitiveness. By carefully evaluating the financial implications and long-term benefits, companies can make informed decisions about investing in automated packaging technology to drive business success.