Summary:
Pneumatic vs Mechanical Ship Unloaders: Compared.
What is a Pneumatic Ship Unloader?
Key Aspects of a Pneumatic Ship Unloader
What is a Mechanical Ship Unloader?
Pros and Cons of Using a Mechanical Ship Unloader
Comparing the Two Methods
Which Should You Choose?
The ocean is perhaps the world’s greatest trade route. Since the West Indies fleets set sail in 1566 across the Atlantic, shipping has driven the world across this area and elsewhere in the world. According to the International Chamber of Shipping, about 11 billion tons of cargo are shipped across the ocean every year. Some of these goods, like grain, need to be unloaded at docks using a pneumatic or mechanical ship unloader. In what follows, we will discuss the differences between these two unloading methods as well as their advantages and disadvantages
The Key Differences
It’s important to note that both these types of unloaders specialize in granular and free-flowing materials like grain. An important difference between a pneumatic ship unloader and a mechanical one is maximum load. In general, pneumatic ship unloaders work best at lower unloading capacities. This is mainly between 400 and 600 tons per hour (t/h). A mechanical ship unloader can handle higher capacities.
There are other differences that set these two apart as well. Pneumatic systems generally have higher maintenance costs. However, they have more sensitive parts that may require additional and more frequent maintenance.
What is a Pneumatic Ship Unloader?
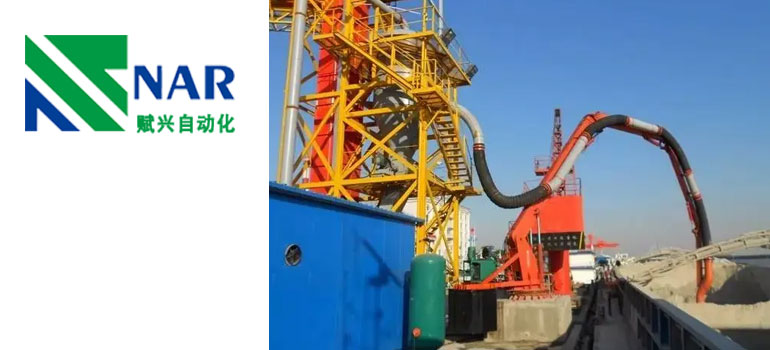
A pneumatic ship unloader is a machine that uses air suction to remove the contents of a ship’s cargo. The machine sucks up the material away from the hold and transports it to a new holding location on the dock. These unloaders work best with materials that weigh less than 1 ton per cubic meter.
Van Aalst invented the world’s first pneumatic ship unloader in 1954. Designed to unload cement from ships, Van Aalst designed the prototype with the goal of reducing dust and spills. By reducing these spills and dust, the company was able to unload the material much more efficiently. The machine could unload at a rate of 20 tons per hour, which was unprecedented in the 1950s. The company later improved the output by 500%. Today, the Van Aalst company’s modern pneumatic unloading machines can remove material at a rate of 800 t/h.
Key Aspects of a Pneumatic Ship Unloader
There are a number of advantages to using a pneumatic ship unloader. The technology has a low investment cost. This means that it’s easier to get started with. The mechanism is also relatively quiet and clean. These machines are also very fast and efficient with the right materials. According to an analysis by Vincent van der Wijk of Buhler Group, pneumatic unloaders can unload product at around 25 meters per second.
However, there are some disadvantages. The system uses telescopic spouts. These raise and lower into the hold where the material is kept. The machine has airlocks and filter systems as well. The number and type of parts used means that more regular maintenance is required to keep them in working order. Accounting for these maintenance costs, a mechanical ship unloader is cheaper than a pneumatic ship unloader in the long term. As a result, businesses must replace parts, and those parts need to be durable to last. This adds additional cost.
What is a Mechanical Ship Unloader?
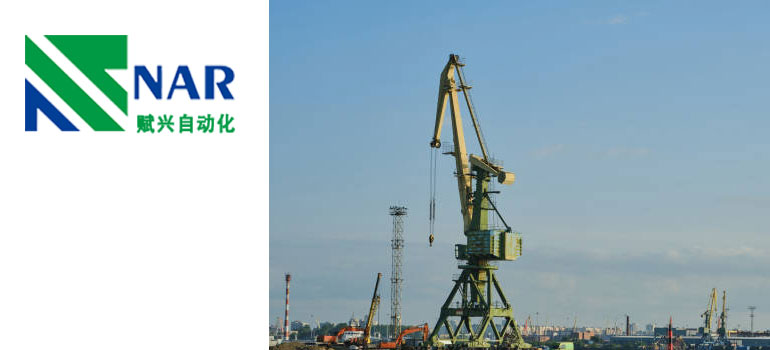
A mechanical ship unloader, also called a continuous ship unloader, is a machine that can extract granular materials from a ship’s hold. One way to do this is through a conveyor. A trusted horizontal boom and a kick-in/kick-out system make up the machine. The conveyor carries the material from the marine side to the dock.
George Hulett of Conneaut, Ohio invented one of the first mechanical unloading systems in 1899. His machine was capable of lifting and dumping 10 tons of iron ore per minute, an astounding feat for the time. The first steam powered machine cost $45,000. Accounting for inflation, this would be worth somewhere around $1.5 million today. The machine went on to assist the United States’ World War II economy greatly. Many consider the machine to have played a major role in the result of the conflict. George was later inducted into the National Inventors Hall of Fame.
Pros and Cons of Using a Mechanical Ship Unloader
There are a number of reasons why these unloaders are often extremely useful. For one, there are more options for removing heavier materials from ships. They function reliably and without as much wear and tear. This means that operating and maintenance costs are significantly less than pneumatic systems. These machines are also less sensitive to foreign matter, making them less prone to error.
However, mechanical systems come at a greater investment cost due to their large size and shape. businesses must plan carefully when working to incorporate a mechanical unloader onto a pier.
Comparing the Two Methods
These two unloading types have various advantages and disadvantages. The type of material impacts the unloading process significantly. When dealing with lighter materials, pneumatic unloaders work much faster than mechanical ones. However, fast isn’t always a good thing. If the product is moving too fast, there’s a greater chance for error and mistakes. Protecting product is important for success.
However, conversely, mechanical systems are more prone to dust from the excavation and dumping process. Pneumatic machines are cleaner and produce less waste. As a result, pneumatic systems can be more efficient in the right context.
However, a mechanical ship unloader will always be more efficient with heavier materials like iron ore.
Which Should You Choose?
It’s a difficult choice. Both types of machines have their strengths and weaknesses. It all comes down to available investment cost and the type of material being transported. A mechanical ship unloader will require a greater initial investment due to its size and bulk. This can be off putting for many businesses, but if installed correctly and used efficiently, it can pay itself off over time and net businesses profits.
However, if your business expects to mainly deal with lighter-weight materials and doesn’t have as much capital to invest initially, a pneumatic ship unloader may be preferred instead. Over time, revenue from receiving operations will be able to cover the higher maintenance costs of the system. However, this means that net revenue won’t be as high.