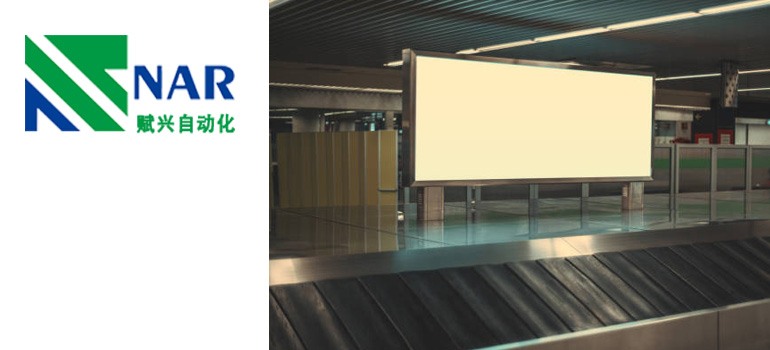
Today’s logistics operations face increasing pressure from all sides. The level of service you expect from a vendor is getting stricter, even as the volume increases. Customer expectations are also growing, especially when it comes to fast and free (sometimes even same-day) delivery. In addition, the boom in e-commerce and the definition of dimensional prices (prices based on the dimension of the package) have led to a greater diversification of types of shipping and individual products.
Manual labor is no longer enough to meet the demands of this particularly challenging environment. The throughput and volume of e-commerce are too high to be handled by manual workers. And all this if you find enough workers to get started – a growing challenge for any order fulfillment operation.
There is, however, a solution for every sorting challenge.
Over the years, sortation conveyor as a means of handling goods and/or shipments has significantly advanced and assumed industry dominance. The increased dependence of industry on automated conveyor sorters is due primarily to the fact that they have had “everything going for them.”
Given the growing need on a global level to find increasingly advanced solutions to sort the parcels to be delivered or to be managed within the warehouses and to allocate them in the most efficient, reliable, and quick way possible, the industry has had to adapt, finding effective and flexible solutions that adequately and intelligently automate the management and sorting processes.
These solutions offer the highest production speeds as well as delicate options for package management.
Elements To Be Considered When Choosing A Sorting Solution
Throughput
Both in standard and peak periods, throughput levels are critical when choosing the optimal technology for automated conveyor sorters. Throughput levels can fuel your return on investment calculations, as well as provide room for operations to scale in the future—an essential consideration for maximizing long-term value.
The perfect automated conveyor sorters solutions are designed to ensure maximum throughput by operating with minimal machine speed. This strategy reduces wear and energy use, increasing the service life of the equipment. It also provides a more delicate handling of the items by reducing the amount of noise in the structure.
Comparison between throughput and speed
It’s easy to get confused between throughput and speed, but they’re not the same. Focusing only on speed, without considering other factors, such as gapping, handling, and accuracy, can lead to inefficient solutions that reduce throughput.
Management Requirements
Another critical factor to consider when choosing a sorting solution is the unique product mix of your operations, and the packaging types used most at your facility. When choosing, consider the entire combination of products, including present and future needs.
The most common factors to consider are the following:
- Types of items to sort – cardboard boxes, shopping bags, plastic bags, padded bags, loose items, etc. Aspects such as size, weight, balance, or shape of the products to be sorted can exclude the use of some sorting technologies.
- Packaging types per item – carton, shrink wrap, clothing packaged in bags, clothing packaged on a hanger, and others. The greater the number of types of things the system can manage, the smaller the number of items that the sortation conveyor cannot manage. And so, the greater the structure’s efficiency, reducing the investment payback times.
Other considerations
In addition to management, throughput, and application requirements, several other factors can significantly impact technology decisions for automated conveyor sorters.
• Surface requirements – many facilities are looking to add e-commerce-oriented solutions to existing buildings, sometimes even in non-public spaces of retail outlets.
• Operating Noise Levels – Some automated conveyor sorters operate at very low noise levels while maintaining very high productivity levels, increasing ergonomic comfort while maintaining throughput.
• Level of investment – some sorting systems require more substantial technologies and supporting subsystems but can prepare for better functioning for future growth.
• Energy use – if energy use is an essential factor in your business, you must ensure you share this concern with the material handling equipment supplier. At the start of the project, usage energy can vary significantly by technology and supplier, depending on the sortation conveyor you decide to go with.
• Levels of competence for maintenance and operator – daily operation and maintenance activities can vary greatly depending on the technology and the MHE supplier. Evaluate how the staff will interact with the equipment and how your current team will be able to maintain the system.
• Future expansion – if it is possible for future growth to take place, this aspect must be taken into account at the beginning of the project. Features aimed at future expansion may be limited by technology or initial system design.
• Deviation Accuracy – Deviation accuracy and the tendency for jams, kinks, and mechanical problems can often depend on the specific design details and gapping requirements studied for the sortation conveyor system you want to use.
• Confirmation of deviation – Confirming a deviation may be a necessary step in some sorting processes, and the methods for doing this may vary depending on the solution.
• Depreciation planning – some sorting technologies may have a longer expected life, affecting the amortization schedule.
The relentless acceleration of e-commerce and intense competitive pressures require today’s order fulfillment operations to leverage as much sorting capacity as possible. In this context, automated conveyor sorters are no longer a luxury reserved for larger systems. Instead, they are a fast-becoming necessity for any company hoping to remain competitive.
While many vendors offer sortation conveyor solutions, it is easy to forget the necessities of your factory, taking into consideration only the fastest throughput rate and the most sensitive package handling options in the industry. So, don’t make this mistake and always look for expertise that goes beyond the latest technology to deliver measurable real-world results.