Summary:
All you need to know about screw unloaders
Composition of screw conveyor
Advantages of screw unloaders
Working process of screw unloader
With the development of mining, port terminals, electricity, cement, and steel industries in China, the transportation volume of ports continues to increase. There is a large market demand for continuous ship unloaders for port bulk cargo. As the main transportation tool for various bulk mineral products, the demand for bulk loading and unloading equipment in various mining markets will continue to grow. Up to now, various models have been developed, and screw unloaders have become the preferred choice for economy, efficiency, and continuity.
Composition of screw conveyor
The screw conveyor mainly consists of metal structure, conveying system, auxiliary working mechanism, operation control system, and other parts. The metal structure includes a gantry and supporting cylinder, a turntable on the cylinder, horizontal support arms, vertical support arms, etc.
The gantry adopts a box shaped structure, and the support legs of the gantry often use one rigid and one flexible support leg to avoid the phenomenon of wheel biting caused by the deformation of the gantry. The rotary support device adopts a rolling bearing type rotary support, and the horizontal and vertical arms can adopt a tubular or box structure. Secondary trusses should be added to horizontal arms with longer horizontal conveying distances to enhance their rigidity. The tail end of the horizontal arm is equipped with a live counterweight to balance the self gravity of the vertical arm and the vertical screw conveyor.
The conveying system of the screw unloader consists of a vertical arm screw conveyor, a relative rotating reclaiming device, a horizontal arm screw conveyor, and a gantry screw conveyor. Belt conveyor systems are generally used behind the dock.
The auxiliary working mechanism of the ship unloader includes the walking mechanism of the ship unloader, the rotating mechanism of the rotating part, the pitch hydraulic cylinder of the horizontal arm and its upper horizontal arm screw conveyor, the vertical arm and its upper vertical arm screw conveyor, and the swing hydraulic cylinder of the reclaiming device.
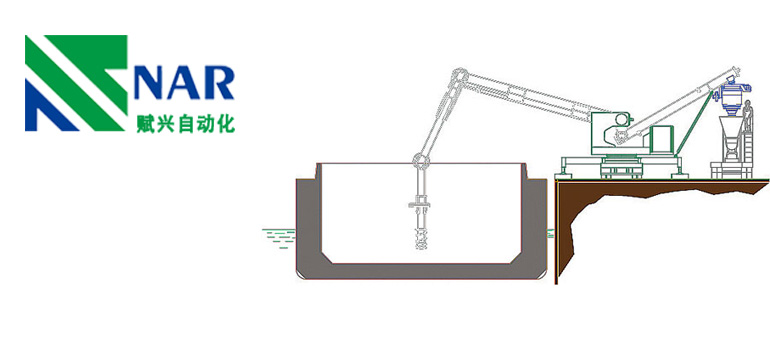
Advantages of screw unloaders
The screw unloader is a type of efficient and continuous bulk cargo unloader, which mainly operates on a horizontal screw conveyor without flexible traction components, a vertical screw conveyor, and a specially designed reclaiming device.
Its biggest advantage is that the operation process is carried out in a closed state, without dust pollution, and its appearance and weight are smaller than other continuous ship unloaders, but its energy consumption is slightly higher. Generally used for unloading loose materials such as coal, cement, bulk grains, fertilizers, potassium salts, etc.
The screw unloader has the following characteristics:
High unloading efficiency. The rated production rate of the screw unloader can reach over 2000t/h. Due to the installation of a reverse rotating material taking device on the ship unloader, the material flows tightly and uniformly in the conveying pipe, and the filling rate of the vertical screw conveyor can reach 70% to 90%. The walking of the gantry of the screw unloader, the rotation of the body, the pitching of the horizontal arm, and the swinging of the vertical arm enable the reclaiming device to reach any position inside the cabin. The reclaiming device also has the function of automatic loosening and excavation. Therefore, regardless of the fluidity of the material, the unloader can continuously work close to full load until there is only a layer of material 30cm to 50cm thick from the bottom of the cabin, and its average production rate can reach more than 70% of the rated production rate.
Strong adaptability to cargo and ship type. Spiral unloaders can be used to unload various powder, granular, and block materials. The vertical section size of the screw unloader is small, and auxiliary mechanisms such as walking, turning, pitching, and swinging ensure the flexible operation of the machine. It can be suitable for various types of barges and seagoing vessels.
Low environmental pollution. The material conveying system of the screw unloader is fully enclosed, and there is no dust flying or leakage of materials or material odors during the unloading operation. For materials such as cement, coal powder, chalk powder, potassium salt, ammonium phosphate, etc. that are prone to air pollution, using a screw unloader is particularly advantageous. The noise of the screw unloader is also relatively small, and the sound level can be controlled below 60dB (A).
Simple structure and low quality. The material conveying system of the screw unloader is composed of a screw conveyor without flexible traction components. The conveyor has no return branch, and its structure is relatively simple. The cross-sectional dimensions of the vertical and horizontal arms are relatively small. Under the same productivity as the target ship, the mass of the screw unloader is much smaller than that of the grab unloader, and it is also the least mass among various mechanical continuous unloaders. Therefore, the cost of screw unloaders is relatively low, and the requirements for the dock’s load-bearing capacity are relatively low.
The wear of working components is relatively severe. The main vulnerable component of the screw unloader is the intermediate support bearing between the conveying screw and the vertical screw conveyor. Due to the relative sliding between the screw and the material, as well as the relative sliding between the supporting screw edge and the bearing in the middle bearing, it is difficult to avoid. Therefore, the main method to improve the service life of the working components is to use materials with good wear resistance, which will increase the cost of the screw unloader.
The intermediate support between horizontal and vertical spirals is a key core technology. We have done a lot of work in structural design, lubrication and sealing, and material selection, and fully absorbed advanced experience and technology from abroad, achieving technological maturity and reliability.
Working process of screw unloader
The flow direction of materials during the unloading process is as follows:
The materials inside the cabin are fed into the vertical screw conveyor through a relative rotating feeding device (counter rotating head).
The material continuously enters the vertical spiral conveyor pipeline and is lifted to the end of the boom, and is transferred to the boom spiral conveyor through the discharge port.
The material enters the transfer funnel located at the center of the rotating tower along the arm frame.
Finally, the material is transferred to the leading edge belt conveyor parallel to the dock through the horizontal screw conveyor on the gantry.
When the screw unloader is in operation, the reclaimer head is inserted into the material pile in the cabin. The reverse rotating reclaimer not only supplies the material to the vertical arm screw conveyor, but also prevents the material from being thrown out due to the centrifugal force generated by the rapid acceleration along the circumference after entering the conveying pipe.
The material entering the vertical arm screw conveyor is lifted and then transferred to the horizontal arm screw conveyor through the discharge port. It is then transported to the transfer funnel at the rotation center, and then transferred to the leading edge belt conveyor parallel to the dock through the gantry screw conveyor. The screw unloader utilizes a material reclaiming device to automatically loosen and excavate materials. It utilizes the movement of the gantry, the rotation of the body, and the pitch and swing hydraulic cylinders to allow the machine head to reach various positions inside the cabin, ensuring uninterrupted and continuous flow of materials with a high filling rate in the unloader conveying system.
The transportation method of materials on the dock can be determined according to the specific requirements of the loading and unloading process. The materials can be transported to the storage yard or silo for temporary storage through a belt conveyor system. They can be directly loaded onto the truck through a loading funnel, or transported to the loading machine and barge through a belt conveyor.